智能硬件产品开发全流程解析
本文通过十八个流程点详解,为大家分享了智能硬件产品研发生产的全流程。
上篇文章我们聊了下软硬件产品经理的那些区别,这篇文章主要分享下硬件产品研发生产的相关流程。
上图所示的是一个智能硬件生命周期内所需要经历的全部流程,以及产品经理需负责的相关工作。下面我们拆解下各阶段的相关内容,以及分享一些相关经验。
一、市场分析
如同互联网产品一样,除了在立项之前需要对市场规模、用户需求、竞品优劣势、BAT布局以及切入的方向进行分析之外,智能硬件还需要分析目标用户的购买力,竞品的定价、利润、上下游供应商、和产品策略等因素。
从而制定产品的目标用户、功能、价位、利润等目标,并分析要做的产品是轻决策类型还是重决策类型,不同类型的产品对售价和产品服务有着很大的影响。同时还要分析制定自己的技术力量和上下的资源整合以及营销策略等。
通过综合分析最后要产出一个包括市场分析报告和项目所需资金、技术方案、人员、周期、利润、营销方案以及产品迭代计划的项目分析报告,并分析得出是否具有可行性,若可行则可进入立项阶段。
我曾经看到一款产品由于前期定了一个不具实现性的目标,且是在当时没有足够的用户规模和购买力的情况下,最后因为技术、成本、售价、市场环境等各方面的压力而最终夭折。
二、立项组建团队
互联网行业有一句话是“好想法是有了,离成功就差一个程序员了”,由此可见对互联网行业来说虽然不是真的只有一个程序员就可以,不过一个项目所需要的成员还是比较少的,一般情况下一个产品、一个UI、一个后台、一个安卓、一个iOS、一个测试基本就是一个标准的产品团队了。
相对智能硬件来说一个团队除了上面说的软件相关人员,还需要组建一个硬件的研发和生产团队,一般至少需要包含ID设计、结构设计、电子工程师、固件工程师、硬件测试、品控、采购、项目经理等角色。
这样看来想要做一个智能硬件所需要的团队至少是需要软件项目的2倍以上的人员。对于如此多的团队成员管理项目的进度也是一大挑战。
软件项目最大的成本也就是人力成本,而对于智能硬件项目来说人力只是成本的一部分,还有一个大头就是产品的模具和开发物料成本,所以智能硬件项目创业将面临着更大的挑战。
如果能组建一个有着丰富智能硬件的团队那么必然就会少踩很多的坑。
三、需求分析
团队组建完后就可以进一步的分析需求了,此时的需求分析是不能像互联网产品那样头脑风暴的,需要根据产品的定位、售价、成本、和技术边界去分析需求,并在成本和体验之间做取舍。
这个时候最重要的是综合需求和成本把产品的形态和硬件配置确定下来,这样后续软件的需求和功能也就可以依托硬件的能力边界去做了。确定好硬件需求后需要把产品的原理图制作好,在验证完可行性之后就可以正式开始产品的设计和研发了。
在这个阶段软硬件的需求和功能需要一同进行规划,达成基本的框架和共识。
等后期硬件确定完后软件部分就根据硬件的边界尽可能的去满足用户的需求,提升产品的体验了,在智能硬件中如果软件做的比较出色,那么也是可以通过较低的成本给产品带来巨大的竞争力的。
四、软件研发
在启动软件研发之前通常是由软硬件产品经理共同设计好产品,输出相应的产品原型和需求文档。有些团队软硬件产品经理是一个,因此需要产品经理和硬件、电子工程师共同设计好硬件的需求并产出相关文档。在这一步完成后就可以开始进入软硬件的开发阶段了。
本章节主要说的软件的研发,其余部分后面再说。产品需求设计好后先由UI设计师进行界面设计,然后再由软件工程师开发出来。
智能硬件产品的软件开发,除了APP和后台之外还有一个固件端的开发,由于固件是要运行产品上的,不过此时的硬件也是刚开始进行研发,所以是无法提供硬件来运行固件的。因此在项目前期固件端的开发通常是先使用开发板来代替产品本身的,等主板设计好可使用时就可以转移到实际产品上进行开发了。
相比纯软件项目,智能硬件从交互上面会更加复杂,所以在三方联调上面会花费更多的时间也会出现更多的问题,因此就需要对产品进行详尽的测试,前期可以使用开发板大致的进行测试,不过由于开发板和实际产品之间还是存在着一些配置等方面的差异的,所以有可能在开发板上没有的问题,在产品上运行时就会出现问题,甚至也有可能是电子工程师给留下的硬件坑,因此在硬件可以运行调试后需要持续对产品进行详尽的测试,要确保产品的稳定性。
通常智能硬件都是可以进行远程升级的,要注意的是在产品出货前一定对升级流程进行多次确认,这样即便软件出现一些BUG也是可以通过远程升级解决的,如果升级系统有问题,那么这个产品别说有BUG修复不了,就连正常的功能迭代都无法进行的。
在硬件产品中通常不会对软件进行无限期的优化和功能迭代,尤其在推出下一代产品之后基本就会停止进行更新。
这主要是因为智能硬件产品是靠买硬件本身赚取的利润,如果一直维护老产品那么就无法与新产品差生差异化,也就无法通过新的功能和体验吸引用户购买新产品,这样厂商也就没有利润可赚取了。
通常硬件产品的设计都是有预计使用寿命的,等产品到达预计寿命后厂商是非常希望用户进行换代的,这个时候人家怎么可能还给你维护产品,增加功能让你继续用呢?
当然也不是所有的硬件产品都是这样的,管道类的产品因为主要谋取利润的点是在内容和服务上,所以这类产品除外,比如智能音箱类产品。
五、ID设计
人都是视觉动物,如果一个产品丑的要命,你还想要畅销那是谈何容易呀!不过对于美和丑不在今天讨论的范围内,今天主要想分享的是ID设计中对成本和产品的影响。
ID设计中有两点需要注意:
第一点:产品外观设计形体必须能开模,其实对于一件产品外观设计完以后能否开模制造出来,取决于拆件。而拆件又与装配循序、外观美观性和成本有紧密关联,比如下面这2组设计。
从形体上来说这两个很不错,但从开模角度来说难度很大,除非3D打印,或者做成软胶强制脱模,否则是没法搞的。
第二点:产品外观设计必须考虑是否能够装配的进去主板或其他电子器件。起码要保证你所设计的产品主板能够放进去你所设计的盒子内部,而且盒子强度也要够。然后你要确保你所设计的产品也能够很好很有顺序的拼装在一起。不要生产出来拼都拼不起那还叫什么设计。
如果ID通过评审就可以通过打手板进行进一步的检验和评估了。在评估OK后即可进行结构设计。
六、结构设计
在结构设计中需要注意根据ID和主板等配件,设计出兼顾两者的内部结构。同时也要考虑产品的坚韧度、组装难度、脱模难度,有运动部件的产品尤其需要注意的是运动部件的结构灵活性和稳定性。
我们之前做的一款产品就曾因运动部件的结构出问题而导致在使用时间稍微久一点或磨具有稍微误差后就会出现阻力增大的问题,最后导致有不少产品进行换货处理,并且曾也增大了模具开发的难度和产品的成品率。
结构设计好后可通过3D打印等技术进行打样拼装,验证其设计如何?
七、PCBA设计
在电子设计和开发中需要注意的是PCB设计和电子元器件选型这两个问题。
第一个是PCB设计时要考虑走线、SMT难度、分离模拟电路与数字电路以及元器件和电路之间的电磁干扰等相关问题。尤其要注意干扰问题,因为这样的问题有时是隐性问题,说不定就在什么时候就会出现。倘若在产品生产大规模后出现那可就尴尬了。
第二个是元器件选型的问题,在电子元器件选中要避免使用偏门的,因为有可能这个元器件随时会面临停产或者与其他元器件难兼容,有时更换一个元器件会因为Pin脚或驱动不兼容而带来大麻烦。对于产品来说使用成熟稳定的元器件不仅能提升产品的稳定性,甚至有时还能降低产品的成本。
在主板设计好后即可进行打板出样品了,样品出来后即可烧录固件对其进行测试和优化
八、整机验证
在这个阶段基本APP、固件、电子、结构都已经出了1.0版本了,此时就可将产品进行整机的组装和验证了。
在这个阶段产品除了要进行各方面的测试验证和迭代优化之外,还需要将产品拿到实际的应用场景和用户那里进行使用测试,这一步不仅可以从用户的角度测试产品的性能,还能暴露出产品场景设计和需求以及产品体验问题,因此这一步是非常有必要的,当产品进一步成熟后再发现问题就很难进行修改了。
在互联网上有很多关于产品经理改需求的段子,而在硬件产品经理圈几乎是没有的。主要是因为硬件产品如果做需求变更的话,那么所需要付出的成本是非常高的。
比如随便开一个模具都是要十几二十万起步,这样高昂的代价谁敢随便需求变更?
再比如对主板进行需求变更,你要知道的是对主板进行一次修改、打板、测试没有个两三周是搞不来的,这样随便搞几个次一两个月就过去,时间这么宝贵谁能经得起这样的折腾呢?
九、包材设计与生产
产品在经过上个阶段后基本外观、功能、配置就已经敲定了,所以此时就可以开始进行包装和说明书的设计和生产了。
如果产品还距离量产的时间还长,那么可以在包材设计打样确认后过一段时间在进行生产,以免因长时间存放导致出现问题。
十、结构开模、电子备料
在产品经过多次测试后,若在ID、结构、电子没有需要改动的情况下模具就开始开模了,电子元器件也可以开始备料。通常开模的时间至少需要2个月以上,所在这段时间内就可以继续迭代优化软件。
在开模这段时间里需要产品经理和结构设计师定期检查开模进度和质量,避免出现较大的进度延迟或失误。
十一、整机验证
在模具进入T1阶段后就可以根据情况进行小批量的生产了,从而进行整机的综合测试。这个阶段主要是针对以下几个方面进行的测试和验证,并输出相关报告和生产指导书。
- 验证模具的质量,生产出来的壳体是否有问题,抗跌落或其他测试否能通过。并对出现的问题进行修复优化。
- 对于电子开始小批量的SMT,验证PCBA的质量,总结SMT的经验和问题,并进行优化改进以及产出生产和测试的方法。
- 包装是否开始生产可视情况而定,若需要进行产品的内侧,有条件的话可以进行小批量的生产。
- 对产品进行耐久性和稳定性等进行多方面测试,找出产品中隐藏的或者需要长时间运行才能发现的问题。
- 产品组装工艺和流程的制定,在这个阶段需要组装多个产品,并对产品组装和生产工艺进行整理,输出产品生产指导书,指导工人生产和生产流程的设计。
十二、产品内侧
产品内侧这一步是非常必要的,建议在任何情况下都不要省去。在产品研发过程中虽然会进行周密严禁的测试,但是依旧不能保证覆盖实际应用中的各种场景。
因此将以上一个流程中所生产的产品交给小规模的目标用户,去真实的场景下进行长时间的使用是可以帮助我们去发现那些我们无法覆盖到的场景和问题。
同时用户使用产品和我们开发人员测试使用产品的方式是不一样的,所以通过这种方式也可以帮助我们找出产品设计中的不足,获得用户真实的使用体验,及时的对产品进行优化。
十三、小批量试产
当经过用户内侧并把发现的问题进行修复验证后,产品研发阶段就正式告一段落了,接下来就要进入生产的阶段了。
开始生产的第一步是选择一个适合的代工厂,在选择时优先选择有相关产品经验且管理规范的工厂,最好相关设备都具备,可以在一家完成SMT、壳体生产加产品组装等相关流程。
如果满足不了这样的条件,那么也要选择有经验管理规范的厂子,至于SMT和壳体生产可以整合其他厂商进行合作,不过这种情况下要注意责任的划分避免出现问题后双方扯皮的事情。选厂时尽量避免那些没有经验,管理松散的小厂,不然以后问题会多了去的。
选好工厂后就要开始与工厂的工程师确定产品的生产流程和工艺了,这一步搞定后就可以开始小批量的生产了。
根据产品类型的不同,生产的数量也不尽相同,不过通常也会生产数百台产品。做这一次小批量试产的目的是为了验证产品生产流程、元器件批量加工、生产工艺和工人的能力等多方面问题,在这一步要对生产流程进行高度的关注,对过程中出现的问题进行总结分析得出解决方案。
同时对产品的成品率进行监控,如果有条件的话可以再次进行一次内测,即便不能进行内测也要多产品进行大规模的抽查使用,以便发现隐藏的问题,模拟客户受到产品的过程和体验。
若在此流程没有什么问题,那么便可进入下一步的正式量产了。此时也要开始对产品进行各方面的认证申请了。
十四、大批量生产
经过试产也就基本没有什么问题与工厂也都应该磨合好了,下面就按照生产排期进行生产即可。不过在这个过程中还是需要相关同事进行驻场监督,以免出现问题不能得到有效及时的解决。
在这里需要对产品的加工处理、员工的操作标准、以及质检的规范程度等方面进行有效的监督和保证,只有这样才可以保证产品不会出现质量问题。
在产品生产的过程中产品经理需要开始编写产品维修手册,准备相应的维修更换的部件,以备售后使用。
十五、销售相关
在生产过程中产品经理还有一个重要的工作要开始执行了,那就是与产品销售相关的工作。这一部分主要包括产品销售材料的制作,比如宣传文件或宣传视频等资料。
同时也要对销售同事进行培训,帮助他们理解产品在市场的定位以及自家产品的优劣势,同教授产品的使用,便于他们进行宣传和销售。
此时还要和售后、技术支持等同事进行培训,告诉他们产品使用方法和可能出现的问题以及应对的方法和话术,并对技术支持进行维修和故障诊断进行培训。
这个时候市场和销售同事就要开始对产品的营销和渠道预热等相关工作了,产品经理需要配合他们完成相应的内容。
十六、量产爬坡
量产爬坡是通过生产流程的优化、提高员工熟练度等方法提升产品的生产速度,在规定的时间内连续大量的生产产品。这个时候需要对产品生产的过程进行全面的监控,保证爬坡的稳定和产品的质量。
当经历过这个阶段后产品就算开始稳定的出货了,此时产品经理算是完成了最重要的使命了,接下来可以松口气,投入到产品的销售和维护等相关工作中了。
十七、售后阶段
在售后阶段除非你产品问题很多,不然产品经理基本就没有太多的事情,主要是做好售后相关同事的培训工作,遇到新问题帮助解决。对于产品销售的数据和市场进行持续的关注即可。
十八、项目维持
在产品的销售和生产都稳定之后基本进入维持的阶段了,此时需要适当的保持产品软件的维护和迭代,对产品进行生产排期等相关工作。
接下就需要对项目进行复盘总结了,分析在项目进行中的各项问题,以及再做项目时如何避免这些问题。
如果产品还有下一代需要启动,那么你就可以着手对下一代产品进行规划开始新的战斗了……
结尾
聊到这里整篇文章也就结束了,希望这篇文章对于软硬件产品经理和硬件产品生产不懂朋友有所帮助。若有不妥之处还请大牛指点。
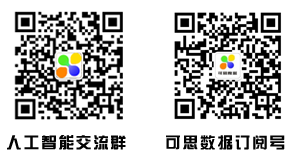
时间:2019-01-26 11:27 来源: 转发量:次
声明:本站部分作品是由网友自主投稿和发布、编辑整理上传,对此类作品本站仅提供交流平台,转载的目的在于传递更多信息及用于网络分享,并不代表本站赞同其观点和对其真实性负责,不为其版权负责。如果您发现网站上有侵犯您的知识产权的作品,请与我们取得联系,我们会及时修改或删除。
相关文章:
相关推荐:
网友评论: