关注 | 机器视觉技术在条包烟外观质量检测上的
导语:提出了一种基于机器视觉技术和可编程控制器(S7-200)的条包烟外观质量检测的解决方案,结合应用实际,具体介绍了系统的工作原理、成像系统运行流程、系统硬件设计、图像处理软件设计以及PLC程序设计等。
现在大多数烟厂已经使用自动装封箱机,但由于原设备上没有条包烟缺陷质量检测器,完全依靠人工来检测条包烟外包装质量,卷烟产品的次品拣出率受人为因素影响较大,条包烟包装质量缺陷事故偶尔发生,影响企业产品商业信誉。
传统的人工来缺陷检测远远不能满足精细生产的需要。当前,机器视觉技术和图像处理技术的在线检测系统正好能完成重复性强,检测精度高的工作。它综合应用了电气、电子、光学、自动控制、计算机、图像处理、机械等相关技术,来实现条包烟外观质量、喷码质量的自动检测和控制,剔除缺陷条包烟。
系统工作原理、成像系统运行的流程图
1、工作原理
条包烟图像检测系统基本原理:在生产检测状态下,条包烟到达预定位置时,同步传感器产生触发信号,通过视觉图像传感器和图像采集卡采集条包烟外观图像,经图像处理软件对图像进行分析,在下一条包烟到达之前,完成上一条包烟的全部分析处理,而喷码的质量检测是由智能相机来采集,并对采集的数码进行智能化处理判断,这两部分检测均给出合格或者不合格的结论,传送至PLC控制系统,如果是不合格品,则由PLC驱动高速气缸将不合格条包烟剔除。
2、成像系统运行的流程图
根据包装机的生产工艺流程,采用顺序检测进行控制,系统程序流程见图1。同步触发传感器信号到达后,视觉图像传感器和智能相机采集烟条外观图像,经图像处理软件对图像进行分析,对采集的数码进行智能化处理判断,进行缺陷判定和统计,并将检测结果信号传送至PLC控制系统。
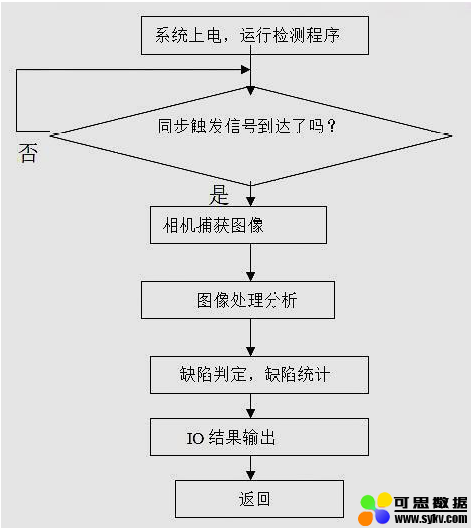
▲ 图1 成像系统运行流程图
系统硬件设备及其功能
根据卷烟制品包装质量控制系统的要求,设计了图2所示烟包质量控制系统。整个系统由上位机、触摸屏、视觉图像传感器、图像采集卡、智能相机、分离装置、触发传感器、LED光源、电磁阀等组成,如图2所示。
(1)图像采集硬件采用丹麦相机JAI-CV-A11和加拿大CORECO公司的图像采集卡PC2-VISION,喷码检测采用康耐视DVT智能相机ISXS-5RC,它们将采集的信号传送给贝加莱工控机APC620。
(2)触摸屏与贝加莱工控机APC620的RS485口通信,实时显示系统运行信息,可设置参数,以及提供多种操作方式。
(3)检测喷码智能相机与贝加莱工业控制计算机使用工业以太网和TCP/IP通信协议通信,在WINDONS-XP下通过运行FRAMEWORK软件编制调试智能相机参数程序。
(4)分离装置由电机驱动,将条包烟减速通过并分离。
(5)触发传感器、光源、电磁阀分别为,光纤放大器FS-21R,光纤探头FU35-FA和NF-DB04,光源组为可变色谱LED摄影灯,喷码检测光源为红色光源,剔除电磁阀选用MAC 公司35A系列产品。
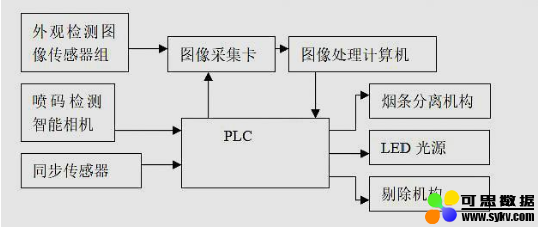
▲ 图2 系统硬件结构框图
图像处理软件设计
1、图像处理软件开发基于Windows XP 下的VC6.0++,图像处理函数库采用Coreco公司的Sapera5.3。
下面针对几种特定的检测功能,简单介绍图像处理软件算法设计原理。
1)错牌检测。
错牌是指其它品牌的烟条偶尔混入到当前流水线中,这是一种严重缺陷,要求接近100%的剔除概率。针对这种缺陷,采取模板匹配的图像处理方式进行检测,实践证明识别准确率比较理想,能够满足实际生产要求。
它的做法是,事先采集相应品牌的特征图片,作为标准模板进行保存,系统工作时,每条经过检测的烟条图片都和标准图片进行模板匹配运算识别,得到当前的相似度系数,通过与预先设定的相似度门限值进行比较,从而判断是否出现错牌缺陷。
模板匹配的数学原理是将模板(子图)与目标区域进行二维相关运算,在设定范围内搜索出相关系数的最大值,再与设定值比较,从而可以判断是否匹配成功,如果匹配成功说明在目标区域存在与标准模板相近似的图案。每一种品牌的烟包装都存在独特的牌号图案,所以一般截取该图案作为该品牌烟条的标准模板。
模板匹配在Sapera函数类库中位于CProSearchArea类和CProSearchEdge类,具体使用涉及几十个成员函数[5]。
2)表面异常检测。
表面异常缺陷是指烟条表面像素出现超出正常范围的灰度值分布,这种情况往往表示烟条表面出现了一定程度的表面缺陷,由于个别像素正常情况下也会出现比较大的波动,因此采用统计指标(均值、方差)来衡量表面异常的程度,根据正常烟条的指标范围设定门限,当出现超过范围的烟条时,系统可以自动判断并剔除。
统计指标计算函数在Sapera函数类库中位于CProBasic类,函数 bool Stats(CProImage& in, float *mean, float *sd, float *min, float *max);
各参数函义:in是待计算的图像,mean,sd,min,max分别是均值、方差、最小值和最大值。
3)拉线缺陷检测。
拉线缺陷包括拉线缺失、拉线歪斜和拉线错牙等几种情况,本系统中采集到的正常拉线的图像特征表现为垂直的线,因此可以通过在设定区域寻找直线的图像处理算法,来检查拉线的完好情况。
判断直线的方法一般采用Hough变换来实现,通过Hough变换可以找出设定区域内直线是否存在以及直线的斜率、数量等参数,综合运用这些参数就可以判断出拉线的各种缺陷。
例如:Hough变换在Sapera函数类库中位于CproBasic 类,Hough变换函数形式为:
bool Hough(CProImage& in, CProImage& out, XformDir direction, int startAngle, int endAngle, float angleIncr, HoughAccumMode accumulate) [6]。
2、防伪喷码检测
针对条包烟上喷印防伪数码过程中出现的“漏喷、模糊、缺字、移位”等质量问题,本系统通过智能相机获取喷印在BOPP包装膜上的防伪数码图象并将其转化为数字信号,采用工控机和软件(FrameWork)技术对图象数字信号进行处理,实现模式识别、坐标计算、灰度分布图、OCR识别、测量等,从而得到所需要的各种目标图象特征值。
再通过系统OCR软传感器对组成数码的每一位字符的形态,特征、像素等参数进行计算测定,并在容许度和其他设定的参数条件范围内通过系统所具有的智能化学习功能对字符的特征进行学习处理,以判别喷印的防伪数码字符的正常表现形态。
并将智能化处理判断结果传给PLC控制系统,由PLC运行用户程序对信号进行逻辑处理,控制高速电磁阀驱动高速气缸,从而控制执行机构完成对超出检测设定的参数条件的不合格条包烟的剔除并报警。
3、自动建模功能介绍
由于每完成一次完整的检测需要人工设置比较多的超差门限参数,比较费时费力,给现场的使用带来不便,因此软件特别设计了自动建模功能,可以帮助人工比较快的找出合适的门限值。
自动建模的工作原理是先打开自动建模功能,然后让一定数量的合格条包烟通过检测器,软件将自动计算和统计该批条包烟的每项指标的分布范围,再按照经验系数自动分配好每个检测门限的默认值,一般情况下再经过人工的简单修正就可以投入使用。
PLC程序流程图
PLC控制系统实时采集输入点信号,并将有缺陷条包烟的结果保持在寄存器LR和HR中,同步移位后进行剔除,如此反复进行完成每条条包烟的自动检测控制工作(见图3)。
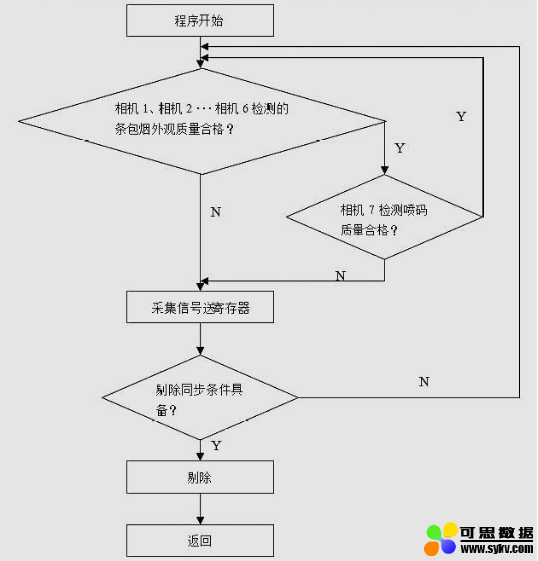
▲ 图3 PLC软件程序框图
结束语
本文主要研究设计了基于机器视觉技术、工业控制机和触摸屏的控制系统,完成了系统中软件、硬件及人机界面设计,通过它们的结合,解决了条包烟外观和喷码质量检测的问题。
在四平卷烟厂YP11A型装封箱机上应用后,系统对条包烟反包、包装错位、无透明纸、无拉线、透明纸皱、条盒翘边、错牌号、喷码漏喷、模糊、缺字、移位等多种质量缺陷的条包烟,对不合格条包烟进行剔除,运行稳定,保证产品质量。
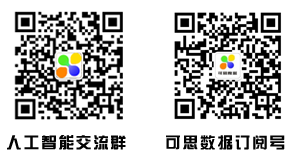
时间:2020-06-27 23:42 来源: 转发量:次
声明:本站部分作品是由网友自主投稿和发布、编辑整理上传,对此类作品本站仅提供交流平台,转载的目的在于传递更多信息及用于网络分享,并不代表本站赞同其观点和对其真实性负责,不为其版权负责。如果您发现网站上有侵犯您的知识产权的作品,请与我们取得联系,我们会及时修改或删除。
相关文章:
- [机器视觉]深度学习与机器视觉的重要性解析!推动机器人摆脱束缚?
- [机器视觉]开启嵌入式智能视觉应用新时代
- [机器视觉]工业视觉发展对图像传感器技术的五大影响
- [机器视觉]2020年中国工业机器视觉行业市场现状与发展前景
- [机器视觉]VisionChina 2021,迎接新发展格局中的“新机遇”
- [机器视觉]机器人和人工智能 助力智慧农业
- [机器视觉]康耐视推出In-Sight 3D-L4000视觉系统
- [机器视觉]凌华科技与英特尔鼎力合作,寻求机器视觉技术
- [机器视觉]凌华科技荣获机器视觉技术领域2020 IoT Innovator大
- [机器视觉]2020年中国机器视觉行业市场现状及发展前景分析
相关推荐:
网友评论: